|
|
1- What is Mineral casting?
2- The advantages of mineral casting.
3- Samples of Pillevaran mineral casting products |
1- What is mineral casting? |
Mineral cast material is a combination of mineral fillers graded according to their size distribution (flour, sand and different grits).
This combination is bonded together using a two component reacting resin system.
Due to the high finishing quality of mineral cast part, large- scale cost reductions are made possible. Mineral casting process has no limits in design and construction and parts with different cross sections connected together can be easily cast, opposite to grey iron that this is considered as a limit.
Machine tools with mineral cast foundations, together with high quality tools, enable higher cutting and axis speeds as well as higher axle acceleration.
There are relevant experiences in particular on the subsequently mentioned fields.
- Machine manufacturing (Cases, Consoles, Bases)
- Manufacturing of pumps (centrifugal pumps)
- Manufacturing of machine tools (Beds, Frames, Tables)
Material properties of mineral cast parts:
Density: 2.3 g/cm³
Compression strength: 105 N/mm²
Bending- Tensile strength: 30 N/mm²
The composition used in Pillevaran Co. consists of casting different size mineral grits and is a new technique specially designed for precise parts .
Pillevaran mineral casting line includes fully automated and mechanized equipment for introducing different minerals, resin and hardener amounts according to predetermined proportions into a mix unit. |
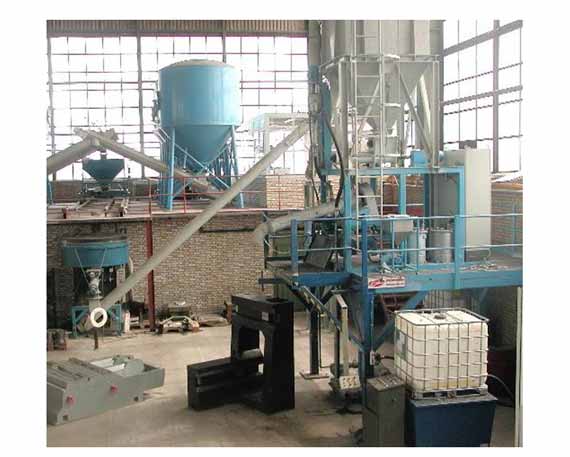 |
|
2- The advantages of mineral casting
- Cost reductions due to
a) Reduction of machining operations as a consequence of better surface qualities.
b) Reduced energy consumption in comparison with energy demand for melting and casting of gray iron.
- High production rate
- Effective in reducing the vibrations
As far as the main resonant frequencies of machines are concerned, mineral cast parts have 6 to 12 times higher damping compared to gray Iran.
- Environmental balance
It begins already in the case of extraction of raw materials. The energy demand for production of mineral cast parts is only 20% per Kg opposite to gray Iran. The energy demands for after treatments of gray iron are not yet considered.Moreover, mineral casting is a clean process.
Extension parts can be easily mounted into the cast part during casting process. Threaded bolts and sockets, hydraulic, pneumatic, cooling and lubricant pipes, guide strips and supports may be easily integrated in the cast parts.
The lower density of mineral cast as compared to gray iron will reduce the construction mass by 20-50% while retaining the same rigidity.
- Chemical durability:
Mineral cast is resistant to oils, emulsions and many other chemicals, e.g. to 15% H 2 SO4 at 80° C.
- High thermal inertia
The high specific thermal capacity and the very low thermal conductivity of mineral cast compared to gray cast iron lead to higher thermal inertia.
This is very important as far as precision tools are concerned. Changes in temperature, especially over short periods have relatively slower and lower impacts on manufactured parts than in the case of gray iron.
Differences in the thickness of the wall have hardly any impact, which is an advantage of cold casting process.
-Geometrical properties
. Surface
It depends on the surface quality of the casting mould. The surface quality of mineral cast is better than grey Iron.Coating for either coloring or corrosion protection are mostly not required.
. Accuracy
Raw mineral cast parts have high accuracy due to lower degree of shrinkage than even compared to grey
Iron.Flatness deviation in planes of mineral cast parts is 0.03 mm/m² and deviations from perpendicular
or parallelism of planes toward each other is 0.04 to 0.05 mm in planes of 1 m². |
|
|
3- Samples of Pillevaran mineral casting products |
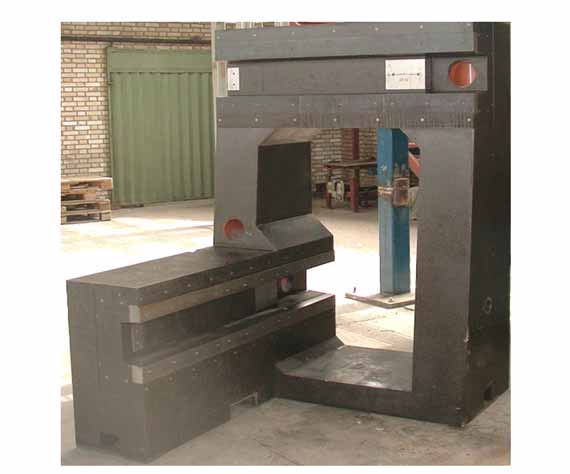 |
Frame of Koerner CNC machine produced by mineral casting |
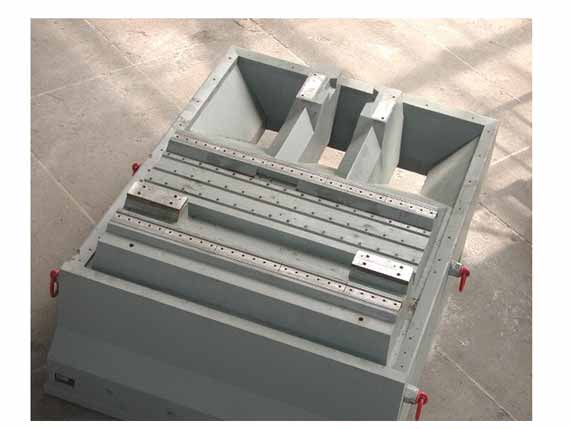 |
Bed of DMG CNC machine produced by mineral casting |
|
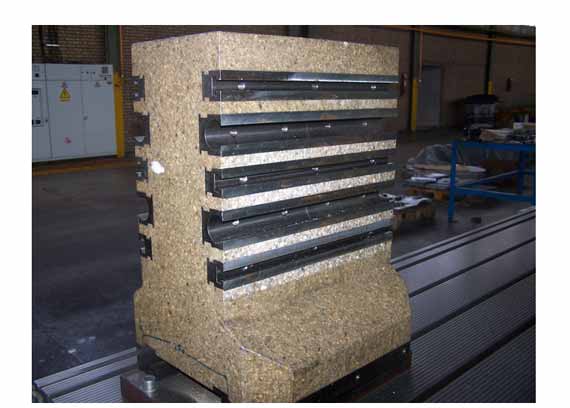 |
Fixture and part clamping system made of mineral cast. |
|
|